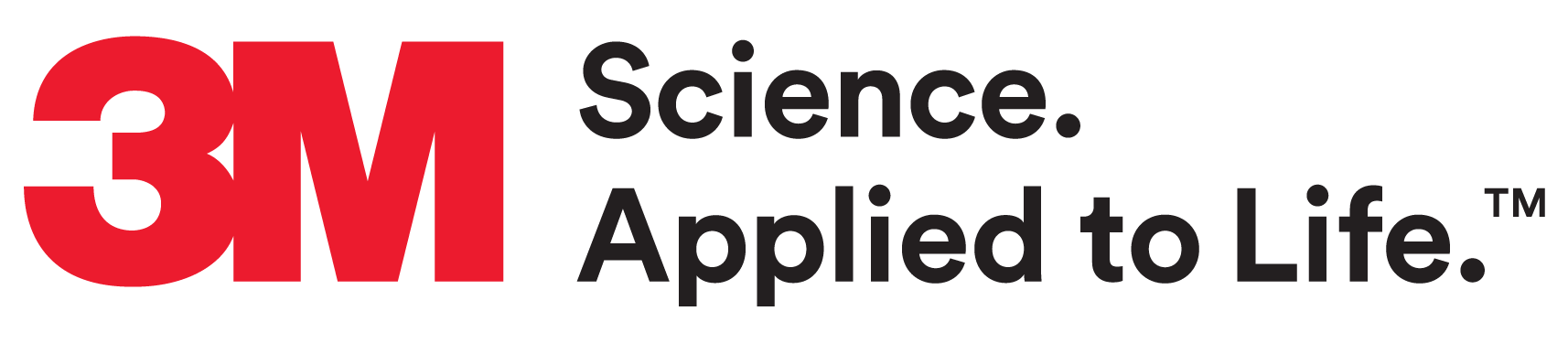
The innovative use of diamond tools for grinding hard materials and CBN tools for machining steel has triggered rapid development in cutting and grinding manufacturing technology that still continues today. As an innovator and pioneer, we support our business partners from industry and manufacturing with individual system solutions so they can meet the constantly increasing international requirements for efficiency and product quality.
That is why we offer for rational machining of hard-to-machine materials (like HSS, high-temperature alloys, tungsten carbide, ceramic, PCD, PCBN, cermets), high quality diamond (DIA) and CBN grinding tools in all bonding systems for every type of application.
Our DIA grinding tools with synthetic resin and metal sinter bonds set new standards for the machining of tungsten carbides. Our DIA grinding tools with vitrified bonding also set new standards for the economical machining of very hard modern materials.
The mass production of precision components cannot be imagined without our CBN grinding tools using vitrified bond in the end. Our CBN grinding tools with electroplated bond technology reach new highs in terms of their grinding process performance in high speed grinding.
Grinding tools with diamond or CBN abrasive grit generally consist of an abrasive coating of grit and bonding material which are applied to a core or wheel body.
For optimal grinding performances, the abrasive grit and bond must be matched so that the abrasive grit are held in the bonding material as long as the grit still has or can form cutting edges. If the worn abrasive grit remains for too long in the bonding agent, the grinding tool loses its efficiency. On the other hand, if the bond wears down before the abrasive grit, then the abrasive grit is not used adequately and the life expectancy of the grinding tool becomes uneconomically short.
Matching the correct bond construction for individual applications allows the highest possible efficiency through the effective use of the grain materials.
That is why it is so important to use a combination of abrasive grit and bond that matches the individual grinding and operating conditions.
- For grinding
- tungsten carbide and steel materials
- High material removal volumes at low grinding forces
- For wet and dry grinding
- High flexibility by mixing in suitable additives
- For fine grinding operations
• Highest wear resistance and
profile retention
• High effective forces and therefore lower material removal volume in
comparison to syntheticresin bonds
• Optimal cost/grinding performance compromise,
mainly for hard metals
• Fast grinding infeed
• Lower wheel wear
• Perfect dressing behaviour
• Used to manufacture abrasive coatings with
defined porosities for an extremely wide range of
applications
• Especially good dressing and profiling capability,
optimally suited for the conditioning of diamond
dressing rollers in particular
• Lower wheel wear, low grinding forces for high
quality workpiece surfaces
• Electrolytic depositing through a layer of grain
on a metallic bodyVery high grip for the highest possible grinding
performance
• For pre-grinding complex profiles with high
material removal volumes
• For finishing grinding with high precision,
for example in the gear-cutting industry
K.S.V. Technologies Co., Ltd.
95/118 Petchkasem Rd., T.Laksong
A.Bangkae Bangkok 10160 Thailand
Phone : +66(0)63-356-6868
Line : ksvtechno
Email : ksv.info@ksvtechnologies.com